Service Type Maintenance
This program lets you maintain services types that are used to identify the type of service or maintenance an asset could require. An asset can have several different service types.
Exploring

This program is accessed from the Program List of the SYSPRO menu:
- Program List > Enterprise Asset Management > Setup


Enterprise Asset Management (EAM) is a comprehensive approach to managing an organization's physical assets throughout their entire lifecycle, from acquisition to disposal. SYSPRO'S Enterprise Asset Management module focuses on the activities required to effectively manage the maintenance of machinery, parts, and other equipment to maximize their value, reduce costs, and ensure they contribute effectively to the organization's goals.

Planned maintenance within the Enterprise Asset Management module refers to scheduled maintenance activities that are pre-determined and performed at regular intervals using a planned schedule. This maintenance is carried out to prevent unexpected breakdowns and ensure continuous operation, regardless of the current condition of the asset.

Unplanned maintenance within the Enterprise Asset Management module refers to maintenance activities that are performed in response to unexpected equipment failures or breakdowns. These are unanticipated events that require immediate attention to restore the equipment's functionality. Unlike planned maintenance, unplanned maintenance disrupts normal operations and often incurs higher costs due to urgent repairs and unavailability of spare parts or resources.
Starting

-
The Enterprise Asset Management module must be installed.


You can restrict access to the eSignature transactions within a program at operator, group, role or company level (configured using the Electronic Signature Configuration Setup program).
Electronic Signatures provide security access, transaction logging and event triggering that gives you greater control over your system changes.

Controls access to the Add function in the Service Type Maintenance program.

Controls access to the Change function in the Service Type Maintenance program.

Controls access to the Delete function in the Service Type Maintenance program.

You can restrict operator access to programs by assigning them to groups and applying access control against the group (configured using the Operator Groups program).

You can restrict operator access to programs by assigning them to roles and applying access control against the role (configured using the Role Management program).

The following configuration options in SYSPRO may affect processing within this program or feature, including whether certain fields and options are accessible.

The Setup Options program lets you configure how SYSPRO behaves across all modules. These settings can affect processing within this program.

Setup Options > Configuration > Manufacturing > Enterprise Asset Management
- Expense accounts only
- Equipment serial mandatory
- Allow zero cost non-stocked components
- Date calculation method for planned jobs

Setup Options > Preferences > Manufacturing > Enterprise Asset Management
- Structure amendment journals required
- Operation amendment journals required
- Structure sequencing required
- Key type
- Default sequence number

Setup Options > Configuration > Distribution > Inventory> Show Warehouses hyperlink
-
Maintenance warehouse
Solving
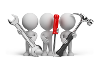
Why don't you drop us a line with some useful information we can add here?
Using

-
Fields on a pane are sometimes removed by default. You can reinstate them using the Field Selector option from the context-sensitive menu (displayed by right-clicking any field in the pane). Select and drag the required fields onto the pane.
The captions for fields are also sometimes hidden. You can select the Show Captions option from the context-sensitive menu to see a list of them. Click on the relevant caption to reinstate it to the form.
If the Show Captions option is grayed out, it means no captions are hidden for that form.
-
Press Ctrl+F1 within a listview or form to view a complete list of functions available.


-
Configure Planned Maintenance Structure
Once the Maintenance Engineer receives a new asset's details, the data to support the maintenance requirements need to be captured:
-
Equipment Type:
Define the types of equipment used within the business and the standard service structures for these equipments types using the Equipment Type Maintenance program.
This enables you to group different Equipment Codes and optionally set a default service structure per group.
-
Equipment Code:
Define the equipment codes to uniquely identify each asset or piece of equipment and link it to a machine, capex project or ledger code using the Equipment Code Maintenance program.
The equipment code is ultimately the master record against which all maintenance activities will be carried out.
-
Service Type:
Define the types of services that are required for every equipment type using the Service Type Maintenance program.
This enables you to supports different service scenarios.
For example:
15 000km service vs. 30 000km service.
-
Service Structure:
Configure the material and operational requirements for every asset and service type combination using the Service Structure Maintenance program.
-
-
Create & Share Planned Maintenance Schedule
Next, the Maintenance Planner will create the maintenance schedule, which is generated by combining the equipment code and service type. This can be set either manually or automatically using forward scheduling options.
Currently, only date-driven scheduling (not run-rate) is supported. For assets requiring service based on run-rate, estimate run times and schedule service dates accordingly.
-
Forward schedule maintenance jobs:
Create the maintenance schedule for each piece of equipment or asset using the Planned Maintenance Job Schedule program.
-
Communicate the schedule:
Share the maintenance schedule with engineers and production teams using the EAM List of Scheduled Jobs report.
-
-
Prepare for Upcoming Maintenance
Once the asset is loaded and its maintenance schedule planned, the maintenance engineer can then review upcoming jobs and their service needs in advance.
-
Use the Planned Maintenance Job Schedule program to assess the service requirements upfront in preparation for upcoming maintenance tasks.
You can also review job operations and related narrations, which can serve as service instructions.
-
-
Review Material Availability
Next, the parts requirements need to be reviewed, to ensure necessary spares are available for the upcoming maintenance jobs.
-
Review availability of materials required for the planned maintenance using the Maintenance Job Parts Review program.
-
-
Issue Material & Labor
The maintenance is then performed as scheduled, with the maintenance engineer issuing spares and labor to the maintenance job as needed.
-
Issue material and labor to the planned maintenance job using the Maintenance Job Issues program.
Based on inventory management practices implemented, the materials can either be requested from inventory (which are then issued to the job) or as they are used.
To support both scenarios, spares can be issued either as a kit or specific issue.
If a kit is issued, unused spares may be returned, and the inventory team will return them to stock (i.e. negative issue).
-
-
Close Maintenance Job
-
Once the service / maintenance job has been completed, the maintenance engineer must then close the job using the Maintenance Job Closure program.
-
Referencing


This lets you enter or select a unique service type code.

Field | Description |
---|---|
Description |
This lets you enter a mandatory description of the type of maintenance service. |
Type of service |
![]() Select this if the service type you are adding is for industrial equipment, machinery or facilities, i.e. an asset that is used in the manufacturing of goods. ![]() Select this if the service type you are adding is for any other type of asset. |
Copyright © 2025 SYSPRO PTY Ltd.